L’AMDEC est une méthode d’analyse des risques. L’analyse des risques est une étapes essentielle de la gestion des projets innovants et l’AMDEC est une des méthodes les plus utilisées.L’acronyme veut dire « Analyse des Modes de Défaillance, de leurs Effets et de leur Criticité ».
- Dans cet article
- D'où vient la méthode AMDEC ?
- Comment quantifie-t-on les risques dans la méthode AMDEC ?
- Quelques exemples
-
Conseils de lecture
D’où vient la méthode AMDEC ?
L’AMDEC est à l’origine une méthode utilisée dans la gestion de la qualité. Elle est aujourd’hui souvent présente dans les projets d’innovation, lorsqu’il s’agit d’identifier les risques d’un projets et les mesures à prendre pour les réduire. AMDEC est la traduction de l’anglais FMECA (Failure Modes, Effects and Criticality Analysis, litt. « analyse des modes, des effets et de la criticité des défaillances »). Comme beaucoup de méthodes de gestion de projets, celle-ci est apparue dans les années 40 dans l’armée américaine, puis a été utilisée dans l’aéronautique.
Comment quantifie-t-on les risques dans la méthode AMDEC ?
Le risque est un aléas, un évènement indésirable dont l’apparition n’est pas certaine, ayant pour conséquence la possibilité que le projet n’aboutisse pas conformément aux objectifs de :
- Date d’achèvement
- Coûts
- Spécifications (techniques, qualité, performance, fiabilité, …)
- Autres : Image de l’entreprise, environnement, juridique, social, …
Dans un projet, il s’agit d’identifier là où il y a un risque de défaillance, de problème. Ce premier travail aboutit généralement à une liste « en vrac », qu’il s’agira de classer ensuite par ordre de priorité. On utilise souvent la méthode du brainstorming pour y parvenir.
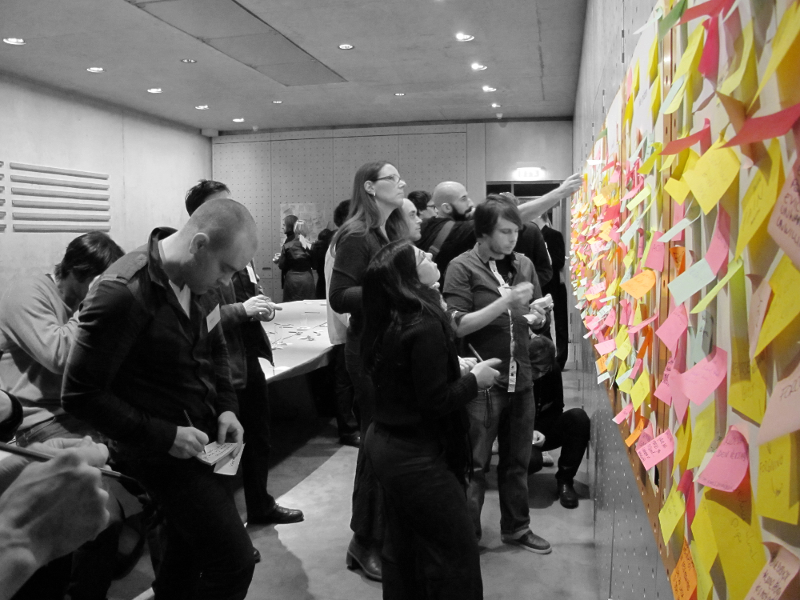
Afin de classer ces risques les uns par rapport aux autres selon une échelle commune, la notion de criticité a été inventée. Cette criticité se détermine généralement par le produit (indice de fréquence) × (indice de gravité) × (indice de détection). Ces indices sont en général définis par le client, ou bien par consensus par un groupe de travail.
Une fois les problèmes les plus « critiques » identifiés, des mesures correctives ou préventives doivent être identifiées (pour réduire la gravité ou bien la fréquence des problèmes). L’AMDEC permet de se poser les bonnes questions très en amont du projet, et donc de prendre dès le début les bonnes décisions de conception.
Qu’elle porte sur un produit, un service, un système, un processus ou un projet dans son ensemble, la réalisation d’une AMDEC doit être collective, exhaustive et systématique. Idéalement, les différents participants représentent des points de vues ou expertises diverses (conception, fabrication, exploitant,…) et ont un pouvoir décisionnel pour engager le cas échéant des mesures correctives.
Pour chaque problème ou défaillance identifié, on évalue :
- sa (ses) cause(s) et son indice de fréquence
- ses effets et l’indice de gravité
- les mesures mises en place pour détecter la défaillance et l’indice de détection
Chaque indice est souvent noté de 1 à 10, le tableau ci-dessous donne un exemple de grille pouvant être utilisée :
Note F | Fréquence ou probabilité d'apparition | Note G | Gravité | Note D | Possibilité de non-détection |
---|---|---|---|---|---|
10 | Permanent | 10 | Mort d'homme ou catastrophe environnementale | 10 | Aucune probabilité de détection |
5 | Fréquent | 5 | Conséquences financières et/ou matérielles | 5 | Un système de détection est en place mais n'est pas infaillible |
1 | Invraisemblable | 1 | Pas grave | 1 | Le système de détection est infaillible |
On calcule alors la criticité : F x G x D
Le but est de hiérarchiser les actions d’amélioration à conduire sur un processus, un produit, un système, un projet en travaillant par ordre de criticité décroissante.
Quelques exemples
Pour exemple, imaginons une machine équipée de pneumatiques, pour diminuer la criticité d’une crevaison jugée inacceptable, on pourrait décider de reprendre la conception et minimiser :
- l’indice de fréquence, en améliorant la structure du pneu, voire en utilisant un pneu increvable,
- l’indice de gravité, en utilisant des roues jumelées,
- l’indice de détection, en équipant le poste de conduite de témoins de pression pneumatique.
Le schéma ci-dessous reprend un exemple d’analyse AMDEC dans un cas « industriel classique » :